Gard Hollinger talks Art, Ambition, and Arch Motorcycle
- Staff
- Apr 15, 2019
- 6 min read
Updated: Oct 28, 2024
by #LizPublika

Long before Gard Hollinger co-founded Arch Motorcycle with Keanu Reeves, he was an eight-year-old kid living on Mulholland Drive and joyriding around the Hollywood Hills on his Schwinn Stingray. One day, Hollinger and a few of his friends combined their skills and built a small bike track in a nearby vacant lot; that’s when Rick, a teenage motocross racer who lived just a few blocks away from Hollinger, showed up and asked if he could ride it. After a couple of laps, he offered the youngster a chance to take his place, sparking Hollinger’s lifelong obsession with motorcycles in the process.
His love of riding motorcycles as well as his interest in how they work evolved in parallel. The first bike Hollinger ever owned, reportedly a purple Taco 22 minibike, was also one of the first vehicles he modified. He seemed to have a real aptitude for mechanics, which soon led him to working as a professional — albeit still very young — marine mechanic on a small island in the Pacific Northwest. Although the kind of work Hollinger was tasked with had very little to do with his love of motorcycles, his affinity for them never diminished.

Throughout his teenage years, Hollinger repeatedly tapped into his natural entrepreneurial talents. By the time he was in his early twenties, he co-founded a small company that “manufactured protective gear for motorcyclists” in Seattle. Though his work commitments kept him busy, Hollinger’s passion for hitting the road led to racing motorcycles, which he did competitively from his early to mid-twenties, even making it to nationals. Because motocross requires riders to maintain and repair their vehicles, Hollinger became even more knowledgeable in how motorcycles are built.
Living a quick-paced and certainly eventful life soon left Hollinger feeling burnt out, and so he put his passion on the back-burner and gave himself a chance to pursue other options. But, it wasn’t long before his interest in motorcycles reignited. After moving back to Los Angeles — trying his hand at acting, and working as a freelance mechanic/fabricator — Hollinger opened up his own shop, Ziggy Harley, in 1997. A few more business endeavors followed, which ultimately led to the founding of LA County Choprods, and the co-founding of Arch Motorcycle — an incredible company that creates stunning custom produced motorcycles.

In a written exchange with ARTpublika Magazine, Gard Hollinger shares his thoughts on Arch, ambition, and the art behind motorcycle design.
Where is your favorite place to ride?
The Santa Monica mountains are my favorite place to ride. It’s the combination of being near the ocean, and being up in the mountains; there is the Malibu canyon, and you can ride all the way up to Mulholland. You can [go] all day and never be on the same road twice.
How did you and Keanu decide to collaborate and launch Arch Motorcycle?
Keanu and I met when he approached me to build him a sissy bar for his 2005 Harley Dyna.

He likes to tell the story of how I essentially turned him down. But, in reality, it became more of a collaboration — with me telling him what I could do to modify and customize his motorcycle instead. He came to my shop and really liked what I was doing. Our relationship grew from there. The bike I modified over the course of a few years became our prototype.
What do you and Keanu bring to the table in terms of expertise? What makes the company efficient?
Collectively, the love and passion for motorcycles is shared. That’s what drives the momentum forward — keeps us pushing the boundaries of motorcycle development and design. But, our ambition and passion for building Arch motorcycles is only possible with the hard work of our team of dedicated craftsmen.
Can you explain what is meant by custom motorcycle? How do you combine old-school principles with emerging cutting-edge technologies and how does 3D technology play into all of this?
[Building a one-of-a-kind bike is risky, because the design may not be 100% tried and true.] The idea behind a custom production motorcycle company is unique. At Arch, we start with an [ergonomically engineered concept/model] that we test for several years. Then, we offer a range of [customizable options from which our customers can choose to personalize their motorcycles]. We make sure that the final products match their individual specifications in terms of fit, color, finish, and the delivery.
The tools we have available today are constantly evolving. Virtual reality allows us to take a theoretical design and bring it to life. [Let’s say an idea] for a motorcycle is sketched on a napkin, we can take that rudimentary sketch and, using virtual reality, turn it into something we can examine as if it were right there in front of us, [which makes working out logistics and making adjustments that much easier.] Technical 3D modeling makes the process efficient. But, it’s actually easy to combine old-school principles with emerging technologies. All you have to do is remember and pay homage to the past.
What is the design for the KRGT-1 based on?
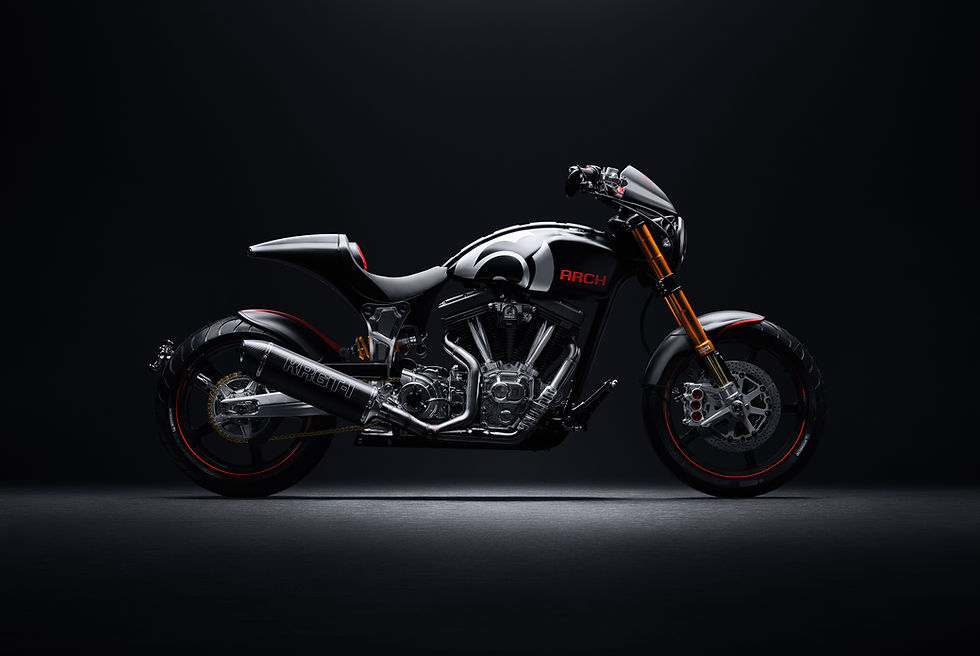
Well, the KRGT-1 is based on the American V-twin.
How are ideas for each of the models conceived? Can you talk about the creative process and inspiration behind your work?
The conception is always driven by what the riding experience should deliver.
The KRGT-1 is not a normal cruiser — it’s a performance cruiser. It’s comfortable, so you can sit on it for a couple of hours, and it is as equally at home on the open roads as it is on the winding canyons.

1S evolved from the KRGT-1s. This elegant model is sport-influenced, with a more aggressive riding position. But it’s still very comfortable, so you can go on longer rides without feeling like you need to stop and stretch.
METHOD 143 was inspired by manufacturers who tend to build show or prototype [vehicles that] never seem to go into production. People can spot these at auto shows; they are often made from some type of clay or printing materials. So, we took the idea and made a concept motorcycle, but it’s actually rideable, and only 23 people will own it.
Forward thinking and engineering artistry has been the foundation of Arch Motorcycle.
Why did you decide to make just 23 METHOD 143 motorcycles?

The number 23 is actually quite interesting; if you look it up, you’ll find that some peculiar superstitions surround it. But, honestly, the thing was that 20 bikes didn’t seem like enough, and 25 seemed like too many. So, we decided on 23.
What kinds of obstacles do you face when you are working on a new fleet?
The main obstacles are regulations. [We need to abide by them] while still maintaining the same integrity and level of design, which we do really well. But, they are part of the joy and sense of accomplishment we experience making beautiful and simple bikes.
How long does it take to create a custom made motorcycle and what types of features are commonly requested?

The typical turnaround is within 90 days of the customer’s order confirmation. As Arch is a custom production motorcycle company, the customer is involved in the entire creative process. [Based on the given direction, we adjust the riding position and the shape of the seat; customize the positioning of the handlebars and the foot position; paint the engines or create special body work.]
Do you think of your work as an art form? What does the future of Arch Motorcycle look like?
We work really hard to maintain the artistic quality of our motorcycles without forsaking the integrity of the mechanical components or riding quality. For us, an Arch motorcycle is a piece of art — but totally and exceptionally functional.
We would like for people all over the world to be able to easily own an Arch motorcycle — it’s the dream. We want people riding Arch bikes through Germany's Black Forest, the South of France, or on the Great Ocean Road in Australia! We want Arch to be available and registered everywhere where people love motorcycles.
Note* Images by Jordan Pay (1,8); Image of Gard Hollinger, courtesy of Arch Motorcycle (2); Images courtesy of Gard Hollinger (3,4), Images of Arch motorcycles by Marcus Eriksson (5,6,7)